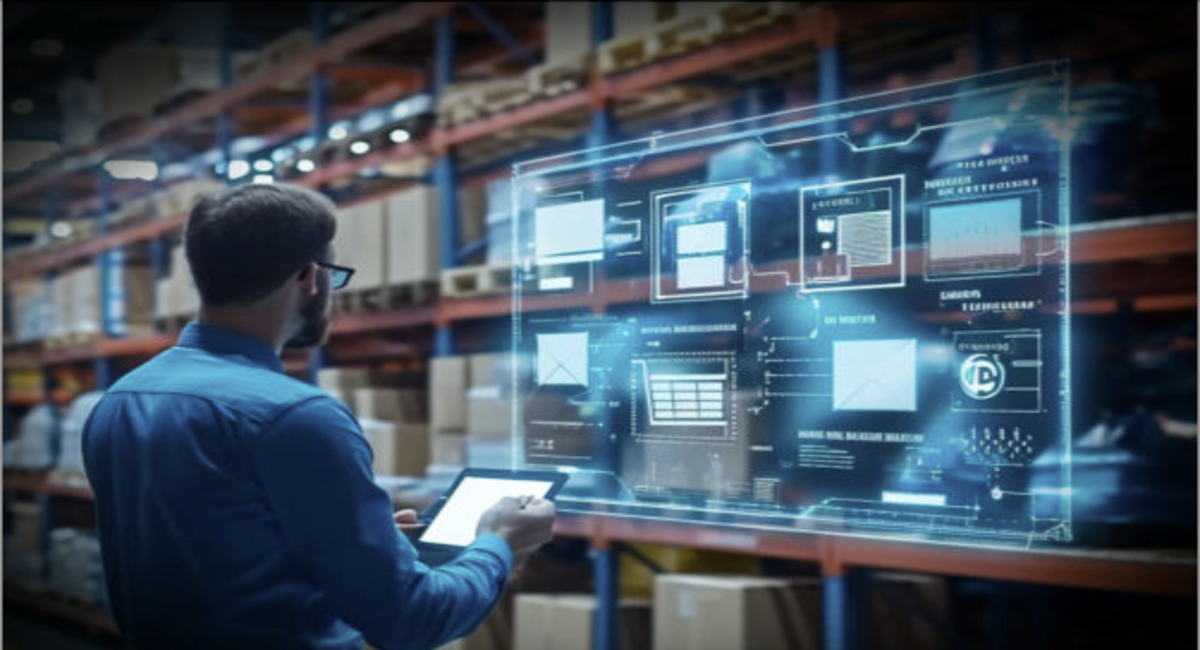
Trasformazione Digitale dei flussi di fabbrica grazie all'introduzione di tecnologie intelligenti, integrate e connesse
Abbiamo aiutato un’azienda specializzata nella produzione di mobili e arredo bagno a superare numerose sfide gestionali grazie all’implementazione di soluzioni di fabbrica intelligenti IoT, sistemi per la pianificazione dei flussi di produzione e magazzino.
L’azienda affrontava diverse problematiche che compromettevano l’efficienza operativa. La gestione del magazzino era basata sull’esperienza dei singoli operatori, senza un sistema standardizzato, causando inefficienze e errori. Inoltre, la mancanza di un sistema tempestivo di segnalazione per il riordino di componenti e semilavorati comportava la necessità di arrestare la produzione per mancanza di materiali e generava extra costi legati al riordino urgente dei componenti. Infine, i tempi di evasione degli ordini erano troppo lunghi, causando insoddisfazione tra i clienti e perdite di opportunità di mercato. Il progetto di innovazione digitale è stato pianificato con una durata complessiva di 9 mesi.
DIGITALIZZAZIONE CATENA DI FORNITURA E GESTIONE STOCK
OTTIMIZZAZIONE PROCESSO DI MANUFACTURING
MIGLIORAMENTO QUALITÀ’ E RIDUZIONE DEI COSTI OPERATIVI
L’azienda, nota per l’alta qualità dei suoi prodotti e l’attenzione al design, si è resa conto che l’evoluzione tecnologica stava cambiando rapidamente il settore manifatturiero. La crescente competizione e la richiesta di soluzioni personalizzate da parte dei clienti richiedevano una revisione dei processi produttivi e della gestione della supply chain. Gli obiettivi principali del progetto erano:
- Digitalizzazione della catena di fornitura e gestione degli stock: Ottimizzare il flusso di materiali e la gestione degli approvvigionamenti attraverso soluzioni digitali. Questo avrebbe permesso di ridurre i tempi di attesa per l’acquisto delle materie prime e migliorare il controllo delle scorte, riducendo i costi di magazzino e aumentando l’efficienza.
- Miglioramento dei processi di manufacturing: La digitalizzazione in produzione è stata pensata per aumentare la visibilità in tempo reale su tutte le fasi del processo produttivo. Implementando un sistema MES (Manufacturing Execution System), l’azienda mirava a raccogliere dati dettagliati sull’operatività dei macchinari, il flusso di lavoro e l’efficienza delle linee produttive. Ciò avrebbe permesso di identificare rapidamente eventuali colli di bottiglia o inefficienze e di agire in modo tempestivo per risolverli, aumentando la produttività e riducendo i tempi di inattività.
- Miglioramento della qualità del prodotto e del servizio al cliente: Implementare sistemi di tracciamento e automazione che permettessero di monitorare la qualità del prodotto lungo l’intera linea produttiva. Un focus particolare era garantire una maggiore precisione nella gestione delle richieste dei clienti, riducendo i tempi di risposta e migliorando la comunicazione.
- Riduzione dei costi operativi: Attraverso una digitalizzazione completa dei processi, l’azienda puntava a ridurre i costi operativi legati alla gestione delle risorse umane e alla logistica, aumentando la profittabilità complessiva.
Per raggiungere questi ambiziosi obiettivi, sono stati implementati diversi interventi strategici e tecnologici:
- Analisi preliminare e mappatura dei processi: Inizialmente, un team di consulenti ha effettuato un’analisi dettagliata dell’intera filiera produttiva e della supply chain, evidenziando i punti critici e le aree di miglioramento. Questa fase di analisi è stata fondamentale per costruire una base solida su cui implementare le successive trasformazioni.
- Implementazione di un sistema MES (Manufacturing Execution System): Il sistema MES è stato adottato per monitorare in tempo reale le attività di produzione. Grazie a questo sistema, l’azienda ha potuto tracciare ogni fase del processo produttivo, dall’inizio alla fine, registrando dati relativi alla produttività, all’utilizzo dei macchinari e alla qualità. Il MES ha anche facilitato l’integrazione dei dati provenienti dai sensori IoT installati sui macchinari, permettendo di raccogliere informazioni dettagliate per la manutenzione predittiva e di ridurre i tempi di inattività.
- Integrazione di sensori IoT (Internet of Things) nelle linee produttive: Sono stati installati sensori IoT su macchinari e attrezzature per monitorare in tempo reale il funzionamento e raccogliere dati preziosi. Questi dati sono stati utilizzati per la manutenzione predittiva, riducendo così il rischio di guasti imprevisti e tempi di inattività della produzione.
- Automazione del magazzino e implementazione di un sistema WMS (Warehouse Management System): Per migliorare la gestione dello stoccaggio e della movimentazione dei materiali, l’azienda ha adottato un sistema WMS, che ha permesso di automatizzare il magazzino. Con il WMS, i flussi di magazzino sono stati ottimizzati e i processi di prelievo e stoccaggio sono stati resi più rapidi ed efficienti. L’uso di robot per il picking e lo stoccaggio ha ridotto il rischio di errori e migliorato l’accuratezza delle operazioni, consentendo all’azienda di rispondere con maggiore rapidità e precisione alle richieste dei clienti.
- Implementazione di una piattaforma di supply chain management in tempo reale: Grazie a una piattaforma digitale per la gestione della supply chain, l’azienda ha potuto monitorare in tempo reale lo stato degli ordini e delle spedizioni. La piattaforma consente di avere una visione globale della catena di fornitura, facilitando il coordinamento con i fornitori e permettendo di reagire prontamente in caso di imprevisti.
Il progetto di trasformazione digitale ha portato a risultati concreti e significativi per l’azienda, migliorando vari aspetti della produzione e della gestione operativa:
- Riduzione dei tempi di produzione del 20%: Grazie all’automazione e all’ottimizzazione dei processi, l’azienda è riuscita a ridurre i tempi di produzione di quasi un quinto, aumentando la capacità produttiva e riducendo i costi associati ai tempi di inattività.
- Riduzione dei costi operativi del 15%: La digitalizzazione ha consentito un controllo più efficace delle risorse e un uso più efficiente dei materiali, con un risparmio complessivo sui costi operativi. La maggiore precisione e velocità nella gestione degli stock ha ulteriormente contribuito a ridurre i costi.
- Aumento della soddisfazione del cliente: Grazie alla capacità di monitorare in tempo reale la produzione e la logistica, l’azienda ha migliorato la previsione dei tempi di consegna e la gestione degli ordini. I clienti hanno beneficiato di una maggiore trasparenza e di tempi di risposta più rapidi, portando a un miglioramento della loro esperienza complessiva.
- Maggiore trasparenza lungo la catena di fornitura: Con la nuova piattaforma di gestione della supply chain, l’azienda e i suoi fornitori lavorano in maniera più coordinata. La visibilità lungo tutta la catena di fornitura ha ridotto i rischi di ritardi o mancanze di materiali, migliorando la pianificazione e la tempestività delle consegne.
- Incremento della qualità del prodotto: I dati raccolti dai sensori IoT e dagli altri sistemi di monitoraggio hanno consentito di identificare e risolvere tempestivamente eventuali problemi nella produzione, riducendo il tasso di difettosità e migliorando la qualità complessiva del prodotto finale.
In conclusione, il progetto di trasformazione digitale ha permesso all’azienda produttrice di mobili da bagno di fare un significativo passo avanti in termini di efficienza, qualità e competitività. La digitalizzazione non solo ha ottimizzato i processi esistenti, ma ha anche preparato l’azienda ad affrontare con successo le sfide future, in un settore sempre più orientato alla sostenibilità e alla personalizzazione dell’offert
I consulenti hanno avuto un ruolo cruciale nel successo del progetto di innovazione digitale. Hanno condotto un’analisi dettagliata dei processi aziendali per identificare le aree critiche e le inefficienze, sviluppando una strategia di innovazione su misura basata sulle specifiche esigenze dell’azienda. Inoltre, hanno selezionato il Warehouse Management System più adatto e hanno guidato l’implementazione, assicurandosi che tutto funzionasse correttamente. Hanno anche fornito formazione al personale per assicurare che tutti fossero pronti a utilizzare i nuovi sistemi e processi. Durante il progetto, i consulenti hanno monitorato i progressi e apportato miglioramenti in corso d’opera, garantendo il raggiungimento degli obiettivi prefissati.
Grazie all’approccio strutturato e alle competenze dei consulenti, l’azienda ABC è riuscita a superare le sue sfide operative e a ottenere significativi miglioramenti in termini di efficienza e competitività