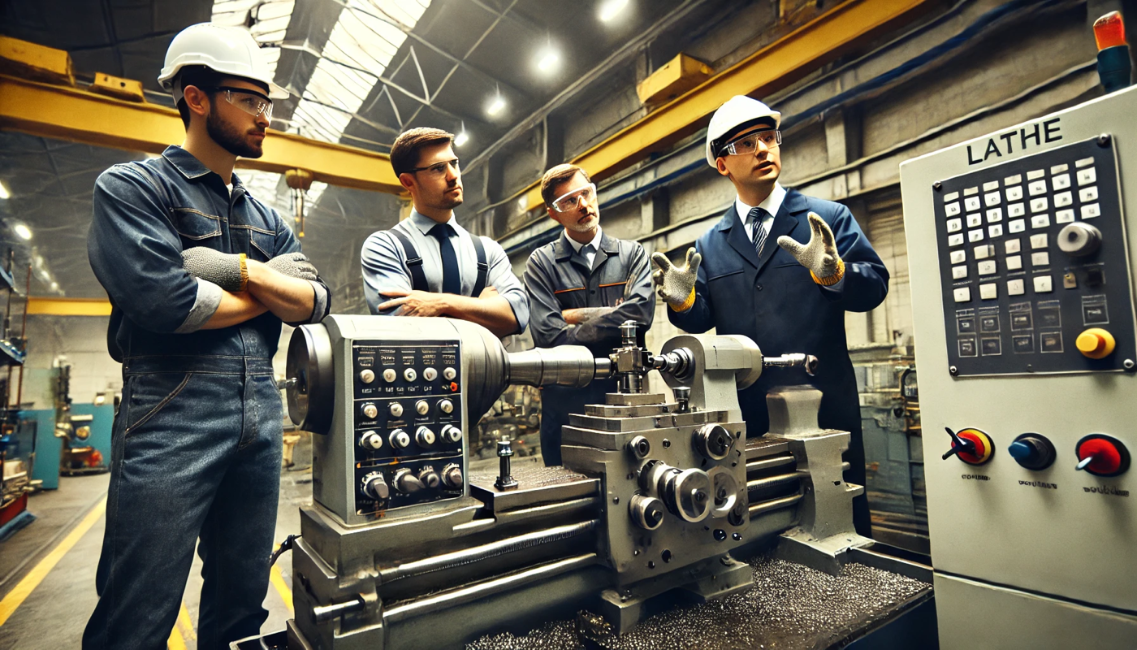
La formazione del personale: una leva per la crescita aziendale
Abbiamo aiutato un’azienda manifatturiera operante nel settore meccanico a ridurre le cause di inefficienza presenti nel processo produttivo, responsabili dei ritardi di produzione e della perdita di competitività
L’azienda
L’azienda è una piccola realtà di tornitura che, per crescere e affrontare le sfide quotidiane, ha deciso di intraprendere un percorso di consulenza con l’obiettivo di migliorare le proprie performance. Il titolare ha identificato due aree critiche su cui lavorare: l’autonomia del personale e l’ottimizzazione dei processi produttivi. La consulenza è stata progettata per affrontare queste sfide e portare l’azienda verso una crescita sostenibile.
La Visione del Titolare
Il titolare dell’azienda ha da sempre avuto l’ambizione di far crescere la propria attività. Tuttavia, ha compreso che per raggiungere questo obiettivo era essenziale affrontare una serie di problematiche interne, prima fra tutte la formazione del personale. Gli operatori non avevano sufficiente autonomia nelle loro attività quotidiane, un aspetto che limitava la produttività e la qualità del lavoro svolto.
RESPONSABILIZZARE E RENDERE AUTONOMI GLI OPERATORI
INCENTIVARE LA COMUNICAZIONE CON STRUMENTI DI GESTIONE VISUALE
PIANIFICARE LE FASI E STANDARDIZZARE TEMPI E METODI
L’approccio si è sviluppato in quattro fasi operative, utilizzando strumenti pratici per migliorare autonomia, comunicazione e organizzazione del lavoro:
1. Analisi e diagnosi → Osservazione diretta (Gemba Walk), mappatura dei processi (VSM) e raccolta dati su tempi e inefficienze.
2. Sperimentazione con il ciclo PDCA → Test su piccola scala di procedure standard (SOP), gestione visuale (Kanban) e autonomia operativa (check-list, formazione problem-solving).
3. Standardizzazione e implementazione progressiva → Definizione di sequenze operative ottimali (Standard Work, SMED), riduzione delle variazioni nei processi e incontri giornalieri per allineamento.
4. Monitoraggio e consolidamento → KPI settimanali, audit interni e Kaizen Events per garantire il miglioramento continuo.
Questo metodo iterativo e partecipativo ha permesso di creare un sistema di lavoro più efficiente e sostenibile nel tempo.
Dopo l’implementazione delle azioni migliorative, è stato avviato un processo di monitoraggio continuo per valutare i risultati ottenuti. I dati raccolti hanno evidenziato un impatto significativo sulle prestazioni produttive:
Riduzione del 50% dei Tempi Morti: L’ottimizzazione del set-up e la migliorata gestione dei materiali hanno ridotto drasticamente i tempi morti dovuti ai fermi macchina e alle attese.
Aumento del 30% della Produttività: Grazie alla nuova organizzazione delle competenze, la produttività degli operatori è aumentata del 30%, consentendo all’azienda di migliorare i tempi di consegna e ridurre i costi operativi.
I nostri consulenti hanno avuto un ruolo chiave in tutto il progetto. Il percorso di consulenza ha avuto un impatto positivo e duraturo sull’azienda. Grazie alla formazione del personale, all’ottimizzazione dei processi e al coinvolgimento attivo di tutte le risorse aziendali, l’impresa ha guadagnato in efficienza, autonomia e competitività. Con una base solida di competenze e processi ottimizzati, l’azienda è ora pronta ad affrontare le sfide future e a crescere in modo sostenibile.